Screw jacks are indispensable tools in various industries due to their ability to move, position and secure loads, yet these devices must also follow certain safety precautions and best practices when being used.
These include proper storage, maintaining them regularly and using them responsibly.
Safety Precautions
Screw jacks are heavy-duty devices designed to convert rotary movement to linear motion and can be used for lifting, lowering, pushing and pulling loads. Available in various configurations, these heavy-duty devices make ideal solutions for industrial and commercial applications alike.
Before using a screw jack, it is crucial to be familiar with its common precautions and safety requirements in order to prevent accidents or damage to the device itself. These rules help reduce incidents related to misuse or abuse.
One thing you should keep in mind about screw jacks is their self-locking worm gears, meaning the system won’t rotate under pressure applied to its lead screw. However, dynamic loading may overcome frictional forces and cause it to rotate anyway.
Screw jack lead screws may either be keyed or unkeyed; when used to fix to loads, an unkeyed lead screw is preferred, while for non-load attachment, keyed leads may be best.
Screw jacks, also known as jackscrews or simply screws, are mechanical devices that use a threaded screw to lift heavy loads. These devices have been in use for centuries and can be found in a variety of applications, from lifting cars in auto repair shops to raising the roofs of buildings for maintenance or construction.
One important consideration when using screw jacks is safety. Improper use or lack of maintenance can lead to accidents and injuries. One potential hazard is the failure of the jack’s components, particularly the screw and nut. Over time, wear and tear can cause the threads to become damaged or worn, leading to instability and possible collapse.
To ensure safety, it’s important to select the right type of screw jack for the job. There are several different types of screw jack available, each with its own unique characteristics and capabilities. For example, ball screw jacks are ideal for high-speed and precise positioning applications, while worm gear screw jacks are better suited for heavy-duty lifting and lowering tasks. Other types include machine screw jacks, stainless steel screw jacks, and miniature screw jacks.
It’s also important to follow proper maintenance procedures to keep screw jacks in good working condition. This includes regular inspections, lubrication of the screw and nut, and replacement of any damaged or worn parts. By taking these steps and selecting the appropriate screw jack types for the job, users can help ensure safe and reliable operation.
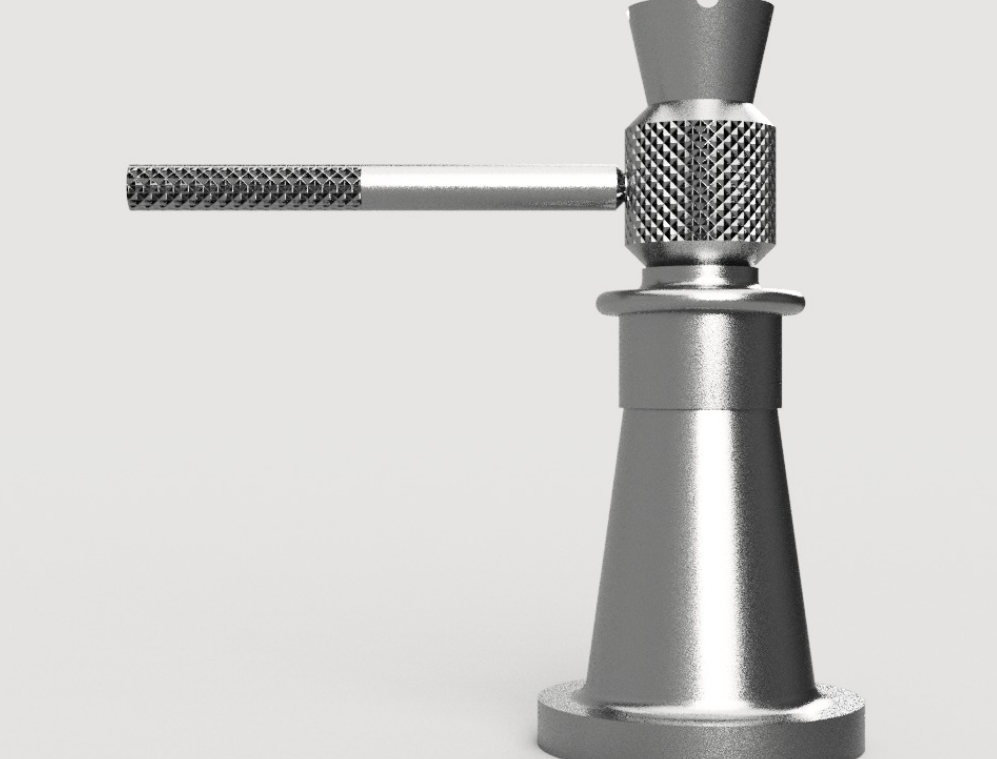
Lifting Loads
Screw Jacks are used to raise, align, position, and hold loads. They’re ideal for use across many applications due to their superior synchronization when compared with pneumatic or hydraulic handling methods.
A screw jack consists of either a machine cut lead screw or rolled ball screw that has been fitted into a worm wheel to convert rotational motion into linear movement. As it rotates, it allows the lead screw nut to slide along as it attaches itself to its load.
If the nut is not secured to the load, friction forces between screw threads may cause it to rotate with it, thus forcing the lead screw to turn with it. Therefore, its end should often be keyed so as not to turn with the nut; similarly it is necessary to key its worm wheel so as not to allow inadvertent rotation by the moving lead screw.
Working on Loads
When working on loads, various kinds of screw jacks can help lift, position, tilt and roll them – such as translating, rotating and keyed screw jacks.
Traveling nut screw jacks use a fixed length lead screw that rotates around its own axis while carrying loads attached to a traveling nut, which moves linearly along its path along the rotating screw.
These jacks are typically employed in applications requiring flush mounting on planar surfaces.
Another alternative is a trapezoidal screw jack, with its rotating worm wheel acting on a lead screw and load attached to its traveling screw which moves linearly along its course as the rotating worm wheel rotates.
Screw jacks are an integral component of automated machinery, with safety and legislative issues driving their use for handling and lifting heavy loads.
Storage

Care should always be taken when using a screw jack; otherwise, any issues that develop can lead to serious damages later.
Threaded spindles must be regularly examined to assess their lubrication conditions (and if needed, recover as required), presence of foreign material, and particularly any corrosive environments that might affect them.
Clean your worm gear screws regularly to avoid build-up of dust and protect them from rust when stored – doing this can extend their lifespan as well as protect them against corrosion.
Screw jacks can be used worldwide to lift, align, position and secure loads safely and reliably, making them the ideal solution in applications where alternative handling methods fail to provide desired results.
Leave a Reply